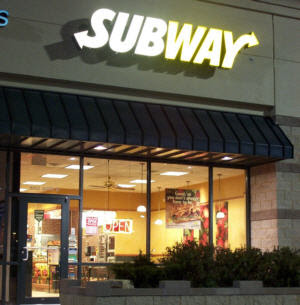
You enter a seemingly healthy multi national food joint which boasts of customizing the nutritious meals or breakfasts, You choose your own breads, sausages, ingredients, garnish etc. to make a perfect sandwich for yourself and pay an amount which you feel is worth paying at for the taste you wanted.
This is exactly what is experienced at SUBWAY.
However as an OPSolute Blogger, I tried to see the operations part behind this experience.
The experience can be termed as a - Perfect Mass Customization in the food industry.
Let us understand this process in detail.
Eg.1)You go to the McDonald's and pick up your favorite burger.
This burger is already prepared, made hot and served to you. These Burgers are prepared on the ASSEMBLY LINE or in-fact this is Mass Production which goes into the preparation.
(Veg Assembly Line and Non Veg Assembly line being a separate assembly line)
Eg.2)You go to the finest authentic MAHARASHTRIAN food corner in the city. You order a Kolhapuri dish an
d it is prepared exclusively for you according to your taste likings and spices choice. This is termed as Mass Personalization. Every time you have been delivered an exclusive product, according to your choice and there are plenty of options through which one can choose.
Eg.3) You Enter Subway.
Step 1 - Select Breads(out of 4)
Step 2 - Select Size (out of 2)
Step 3 - Select stuffing (out of 8)
Step 4 - Select sauce (out of 6)
Step 5 -Select the way it is served (Grilled or Plain)
In this case one can choose from a few sub-items and prepare a wide range of items according to the choice of the customer.
This is the Mass Customization Principle which goes for a food industry.
I shall explain this in detail.
What is Mass Customization:-
Subway produces high volumes of subs or meals. However it has few raw materials towards making the end products. The variety of these end items is high.
It is the creation of high volume product with large variety so that a customer may specify model of his exact requirements of a large volume of possible end items arising from a few raw materials.
Why Mass Customization:-
Customers have a varying food taste. It is highly impossible to serve them satisfactory and profitability without mass customization.
Mass personalization is very costly and time consuming and would have constraint on the output volumes.(eg. you go and stitch a shirt for you)
Mass Production would not target the varying consumer tastes and would refrain a food place like SUBWAY being a market differentiator.
Also a customized experience would ask for a premium pricing profitable for a firm.
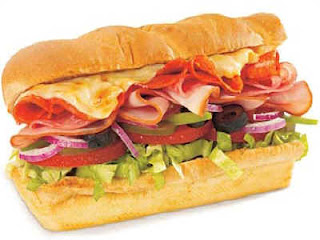
What is needed for Mass Customization:-
One needs to have following three things to implement Mass Customization-
1.Product Modulation
2.Process Modulation
3.Supply Chain Integration
1. Product Modulation-
The subs, meals, or footlong sandwiches in the SUBWAY menu can be product modulated. Each of these end items have distinct ingredients which are
A product modulation means that a product can be broken down into its system ingredient parts. These are separable and form basic building blocks towards the finished product.These parts can be subassemblies, subparts or an ingredient part. The constituent parts have distinct characteristics, features and different components characterized different end products or features of the end products.
By product modulating the subway systems, once can produce number of different products.
Statistically speaking, by multiplicative theorem Subway can have 4*2*8*6*2= 576 unique subs.(Breads(out of 4), Select Size (out of 2),Select stuffing (out of 8), Select sauce (out of 6), Select the way it is served (Grilled or Plain - out of 2)
(However many of them are functionally identical or are redundant or in simple terms, NOT TASTY NOT FEASIBLE kind of..)
2.Process Modulation
All Subway menus are process modulated. Making a sandwich/sub being a simple process, modulation is easy and directly implemented.
A process modulation means that the process is so flexible and changeable that all processes can be inter-changeable and can be done without a lot of human resource.
3.Supply Chain Integration
Supply chain for subway typically will consist only of Procurement, Production and Self delivery. As there are few raw material towards the finished product, the procurement process is standardized and can be managed easily without managerial interference.
Supply chain integration consists of collaborative procurement taking into consideration the daily consumption.
So this is what the FootLong Mass Customization Experience is all about.
So when you go next time, for a sub, just think about the FOOTLONG Mass Customization behind the sub..!!